(P V C) tube.
From the perspective of the groove, it is divided into a work space trunk, a horizontal trunk line slot, and a vertical trunk line slot. What kind of material is used, according to
User needs, investment to determine.
Metal pipe laying
(1) Processing requirements for metal tubes
The metal pipe used in the integrated wiring project shall comply with the provisions of the design documents, and the surface shall be free of perforations, cracks and obvious irregularities.
Uneven, the inner wall should be smooth and no rust is allowed. Pipes of sufficient strength should be used where they are susceptible to mechanical damage and when buried directly under heavy loads.
The processing of metal pipes shall meet the following requirements:
1) In order to prevent the cable from being scratched when the cable is worn, the nozzle should be free of burrs and sharp edges.
2) In order to reduce the shearing force on the cable at the nozzle of the straight buried pipe during the sinking, the metal nozzle should be made into a trumpet shape.
3) After the metal pipe is bent, there should be no cracks and obvious concave sag. Excessive bending will reduce the effectiveness of the metal tube
The pipe diameter makes it difficult to wear cables.
4) The bend radius of the metal tube shall not be less than the minimum allowable bend radius of the cable being penetrated.
5) Anti-corrosive paint should be applied to the galvanized pipe zinc layer peeling to increase the service life.
(2) Metal tube cutting thread
When piping, the pipe should be cut according to the actual length required. The pipe can be cut with a hacksaw and a pipe cutter.
Or electric motor pipe cutting machine, gas cutting is strictly prohibited.
The pipe and the pipe are connected, and the pipe and the junction box and the wiring box are connected, and the end of the pipe is required to be threaded. Welded steel pipe
Threading, can be used for pipe stranding (commonly known as silk) or electric pipe threader. Hard plastic pipe threaded wire, available in round wire.
When the wire is threaded, the pipe is first fixed on the pipe pressure, and then the wire is lapped. If the electric Threading Machine is used, the work efficiency can be improved.
After the wire is finished, the nozzle should be cleaned at any time, and the burrs on the end face and the inner wall of the nozzle should be honed with a trowel to keep the nozzle smooth, so as not to cut the cable insulation sheath.
(3) Metal tube bending
The elbow should be minimized when laying metal pipes. The elbow of each metal pipe should not exceed 3, and the right angle elbow should not exceed 2
There should be no S bends. Too many elbows will make it difficult to wear cables. Cables with larger cross sections are not allowed to have elbows.
When the actual construction can not meet the requirements, you can use a tube with a larger inner diameter or a cable box at the appropriate location to facilitate the cable.
The bending of the metal tube is generally carried out using a bender. First place the front section of the pipe where the bend is required in the bender.
In the direction of the back or side of the bending direction, to prevent the tube from being bent, then use the foot to step on the tube, bend the hand bender, and gradually move the bender so that the required curvature can be obtained. The bending radius should meet the following requirements:
1) When it is clearly matched, it is generally not less than 6 times the outer diameter of the pipe; when there is only one bend, it is not less than 4 times the outer diameter of the pipe;
At the turn, bend into a concentric circle.
2) When it is darkly matched, it should not be less than 6 times of the outer diameter of the pipe. When it is laid in underground or concrete floor, it should not be less than the outer diameter of the pipe.
10 times.
In order to facilitate the threading, when the horizontally laid metal pipeline exceeds the following length and is bent too much, a cable box or a connection should be added in the middle.
Wire box, otherwise you should choose a larger diameter.
• When the pipe is not bent, the length can reach 4 5 m;
• When the pipe has 1 bend, the straight line length can reach 30 m;
• When the pipe has 2 bends; the length of the straight line can reach 20 mm;
• When the pipe has 3 bends; the length of the straight line can reach 1 2 m;
When the pipe diameter exceeds 50 m, a pipe bender or a hot boring method can be used.
• The pipe of the concealed pipe should be smooth and with an insulating sleeve. The extension of the nozzle should be 25 to 50 m.
(4) The connection of metal pipes shall meet the following requirements
The metal pipe connection should be firm, the seal should be good, and the two nozzles should be aligned. Length of sleeved short sleeve or threaded fitting
It should not be less than 2.2 times the outer diameter of the metal tube. When the metal pipe is connected by short sleeve, the construction is simple and convenient; the pipe joint thread is adopted.
The connection is more beautiful, ensuring the strength of the metal tube after connection. Either way, it should be firm and sealed.
After the metal tube enters the junction box of the information socket, the buried tube can be fixed by welding, and the exposed length of the tube into the box should be less than
5 m m. The tube is fixed with a lock nut or a cap, and the thread of the lock nut is 2 to 4 buckles.
The position of the metal pipe nozzle leading to the wiring closet should be easy to connect with the cable. The metal pipe nozzles laid side by side shall be arranged in an orderly manner.
Easy to identify.
(5) Metal pipe laying
1) The concealment of metal pipes shall comply with the following requirements:
• The inner diameter of the metal pipe embedded in the middle of the wall should not exceed 50 m, the pipe diameter in the floor should be 15 to 25 m, and the dark wire box should be placed at the line of 30 m.
• Metal pipes laid in concrete and concrete should be solid, flat and should not be sunken to ensure the laying
The cable runs safely.
• When the metal pipes are connected, the pipe holes should be aligned, the joints should be tight, and no water or mud should penetrate. The tube hole is aligned without misalignment,
The effective management of the pipeline is not affected, and the laying of the cable is ensured smoothly.
• The metal pipe should have a drainage gradient of not less than 0.1%.
• The buried depth of the metal pipe between the buildings should not be less than 0.8 m; when laying under the sidewalk, it should not be less than 0.5 m.
• Pull wires or pull wires should be placed in the metal pipe.
• Both ends of the metal tube should be marked to indicate the building, floor, room and length.
2) Metal pipes shall meet the following requirements when applied:
The metal tube is clamped with a clamp. This type of fixing is more aesthetically pleasing and easy to disassemble when it needs to be disassembled. Metal support point
Spacing should be designed according to the requirements when required. No more than 3 m should be required without design requirements. The tube is secured with a pipe clamp at a distance of 0.3 m from the junction box. In the elbow, pipe clamps are also used on both sides of the elbow.
3) When the optical cable and the cable are laid in the same tube, the plastic sub-tube should be preset in the concealed pipe. Laying the cable in the sub-tube to make the cable and electricity
The cables are laid separately. The inner diameter of the sub-tube should be 2.5 times the outer diameter of the cable.
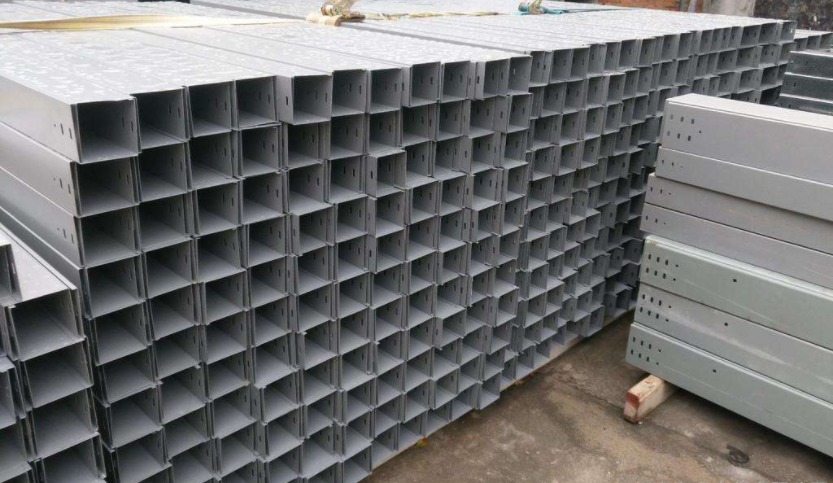