At the beginning of photovoltaic industry, in order to promote the development of photovoltaic industry, the government launched a series of subsidy programs. Under the nourishment of high subsidies, photovoltaic enterprises in various regions have sprung up. However, due to the lack of technical level and industry experience, the photovoltaic industry in the past There are many problems in the rough development of the company. Most enterprises have problems such as backward production capacity, "fraud compensation", and poor quality. The embarrassment of low-quality development has attracted the attention of the government.
After a series of policy adjustments such as tightening subsidies and formulating industry qualification standards, my country’s photovoltaic industry has gradually moved towards a path of high-quality development since 2017. Leading companies in the industry have cleared the industry through technological innovation and cost control. Redundant capacity and low-quality products successfully calmed down the industry. Since then, the photovoltaic industry has ceased to be hot, and capital has ceased to pursue it.
What is the cause of the sudden rise of this round of photovoltaics? Where will it go in the future? Which companies will benefit from this? We may need to observe the overall situation from an industry perspective.
he logic of photovoltaics
Polysilicon, whose price advantage is no longer prominent, is gradually being replaced by more efficient monocrystalline silicon
The core logic of the photovoltaic industry mainly depends on "cost" and "subsidies."
For downstream power generation companies, the duration of sunshine (i.e. light receiving rate) is roughly fixed. Under the condition of fixed annual output value (i.e. power generation), the control of marginal costs and revenue is the key to the profitability of the company, and the purchase of photovoltaic modules An important part of the composition of the operating costs of downstream enterprises naturally greatly affects the profitability of enterprises.
The photovoltaic modules purchased by downstream power generation companies generally go through three production links. The first link is the "silicon-wafer" raw material stage. The most well-known of these is the horizontal competition between monocrystalline silicon and polycrystalline silicon.
Photovoltaic industry initially had backward process technology, low production capacity of monocrystalline silicon with higher photoelectric conversion efficiency, but high cost. Therefore, monocrystalline silicon left an impression of high quality and high cost in the early days.
Compared with monocrystalline silicon, the cost of polycrystalline silicon is quite friendly. Since polycrystalline silicon is processed through ingot casting and other processes, its raw material requirements are not as stringent as monocrystalline silicon. Most silicon scraps, scraps and even monocrystalline silicon All defective products that fail to process crystalline silicon can be re-synthesized into polycrystalline silicon through the casting process. Compared with monocrystalline silicon, polycrystalline silicon has obvious cost advantages. However, due to its purity, the photoelectric conversion efficiency of polycrystalline silicon is 3-4% lower than that of monocrystalline silicon on average.
Since then, due to the simultaneous existence of market demand for high efficiency and low prices, high-quality, high-priced monocrystalline silicon and low-quality, low-priced polysilicon have formed a pattern of dividing rivers.
However, with the development of the industry and the advancement of technology, the pattern of ruled by rivers has been gradually broken, which also involves the second production link of photovoltaic products, "silicon wafer-panel".
The inherent differences in physical properties of monocrystalline silicon and polycrystalline silicon can be compensated by process and technology in the process of making solar panels. For today's photovoltaic industry, it has benefited from the development and improvement of PERC, diamond wire cutting, and texturing processes. The photovoltaic conversion efficiency of solar panels using monocrystalline and polycrystalline silicon wafers as carriers has been improved, while the cost of both has dropped again and again. Take the diamond wire cutting process as an example. Compared with the previous mortar steel wire cutting process, the new technology has 4-5 times higher efficiency (cutting speed) and less loss (increased output by 15-20%). This makes the application cost of monocrystalline silicon gradually reduced.
However, since polysilicon is already a low-cost and low-margin queue, its marginal utility in reducing costs in the process of process improvement is not as good as that of monocrystalline silicon, which has gradually narrowed the cost gap between the two.
Taking market share as an example, the market share of monocrystalline products has jumped from 5% in 2014 to about 60% in 2019, which also shows that polycrystalline silicon, whose price advantage is no longer prominent, is gradually being replaced by more efficient monocrystalline silicon. Replaced.
And the third link is only the assembly process of "panel-photovoltaic modules", which involves various accessories such as inverters, backplanes, and brackets in addition to silicon panels. In the process of continuous decline in the cost of solar panels, the cost of various accessories has gradually increased. Since 2012, the cumulative cost of solar panels in photovoltaic modules has decreased by more than 40%, while the total cost of accessories has only decreased by 10%-15%. It can be seen that the solar panels are still the top priority in controlling the cost of photovoltaic modules.
The general increase in the market this time is due to the price increase at the source of the solar panel chain. According to the data released by the China Nonferrous Metals Association, due to the suspension of production and maintenance of silicon material manufacturers and the Xinjiang epidemic, the supply and demand of silicon material has a serious imbalance between supply and demand. The average price of silicon raw materials increased by 5.73% month-on-month, which affected the whole body. The rise in the source naturally led to the restlessness of the entire industry chain. The prices of single, multi-silicon wafers and midstream solar panels also rose accordingly.
However, from the perspective of the profit model of the photovoltaic industry, the source of downstream profits is mainly the anchored state grid price and government subsidies. For most photovoltaic companies, the only way to improve efficiency is to determine the production capacity (power generation). On the basis of lowering the cost rate, if the upstream comprehensive cost continues to rise and the company’s power generation cost per kilowatt-hour is greater than the grid-connected + subsidy income per kilowatt-hour, the purchase willingness of downstream companies will be reduced.
At this point, we will find that it may be slightly wrong to judge industry revenue and company performance only by the increase in material prices. According to the latest grid-connected acquisition and subsidy policy in 2020, taking distributed self-use power generation subsidies as an example, each kilowatt-hour Since the subsidy of 0.1 yuan/degree was lowered to 0.05 yuan/degree in 2019, thanks to the healthy development of the industry, the downward trend of subsidy amounts has not changed.
It can be seen that downstream power generation companies cannot withstand the endless rise of upstream related costs without bargaining power. If the company’s future development is judged only by the increase in revenue brought about by price increases, it must be highly probable. There was a misjudgment.
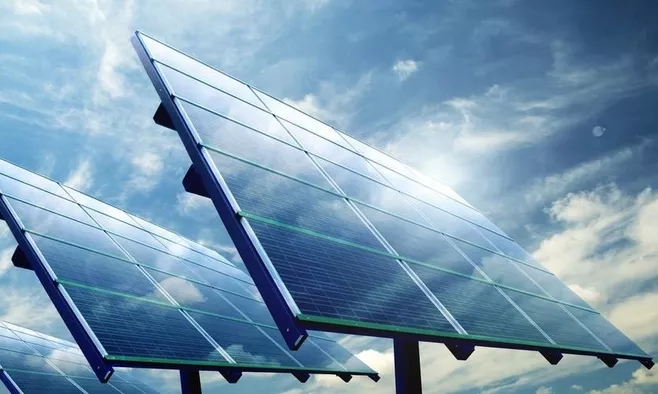